熟料矿渣混合粉磨,熟料破碎及图纸
概述: 在水泥生产中,粒化矿渣尽管已成为水泥第二组分,但是其潜在活性远未得到充分发挥,矿渣水泥早期强度低为其例证。粉碎机械力化... 免费询价!
熟料矿渣混合粉磨,熟料破碎及图纸尽在上海矿山破碎机网, 上海矿山破碎机网提供沙石厂粉碎设备、石料生产线、矿石破碎线、制砂生产线、磨粉生产线、建筑垃圾回收等多项破碎筛分一条龙服务。

在水泥生产中,粒化矿渣尽管已成为水泥第二组分,但是其潜在活性远未得到充分发挥,矿渣水泥早期强度低为其例证。粉碎机械力化学研究表明:粉磨过程不仅是粒子的细化过程,而且熟料矿渣混合粉磨,熟料破碎及图纸还往往伴随有物料物理化学性能的改变,亦该过程可提高材料的活性。通过优化粉磨过程,可提高矿渣水泥浆体强度,熟料矿渣混合粉磨,熟料破碎及图纸比采用改善熟料矿物组成或添加激发剂等,以提高硬化水泥浆体强度的措施更为简便易行。所用的熟料密度为g/cm,个率值分别为:硅度铝率石灰饱和系数。
试验用双仓球磨机规格为mxm,填充率为%,转速为r/min,制样方式有:矿渣熟料石膏单独粉磨后混合,混合操作在混料机中进行,混合时间为min;矿渣熟料石膏混合粉磨;矿渣预挤压后混合粉磨。预挤压矿渣的制备方法为:将一定量的经过缩分干燥的矿渣通过辊压机,分别在MPa150MPa200MPa的压力下将矿渣压成料饼,再把料饼打散,得到预挤压矿渣试样。
熟料混合粉磨
水泥浆体强度测试方法为:按标准稠度用水量,采用mmxmmxmm净浆试块,手工搅拌振动成型标准养护。在研究单独粉磨混合粉磨以及矿渣预挤压后,混合粉磨种工艺对矿渣水泥产品细度的影响,当不同矿渣掺量下,以比表面积经时间变化,表示出混合粉磨效率试验结果。其效果:熟料单独粉磨的效率远大于矿渣单独粉磨效率;将熟料和矿渣混合粉磨时,随矿渣掺量的增加,粉磨效率逐渐降低,但降低的幅度并不与矿渣掺量成比例。如矿渣掺量为%时,混合料粉磨的比表面积变化曲线接近于熟料单独粉磨,而当矿渣掺量为%时,混合料的细度变化趋势则近似于矿渣单独粉磨,说明随矿渣掺量的变化,混合料的粉磨特性也发生了变化。由上述实验结果可以得到以下初步结论:从粉磨细度考虑,当水泥中的矿渣掺量小于%时,混后粉磨工艺可提高产品比表面积;当矿渣掺量大于%时,采用单独粉磨后再混合的工艺将优于混合粉磨工艺,但若用矿渣预挤压后混合粉磨工艺则更佳。矿渣掺量为%时,混合粉磨产品的粒度分布曲线与熟料单独粉磨的曲线很接近,而同熟料和矿渣单独粉磨后再混合的产品粒度分布曲线相比,混合粉磨的物料呈现软特性,其产品粒度细于单独粉磨后苒混合的产品。
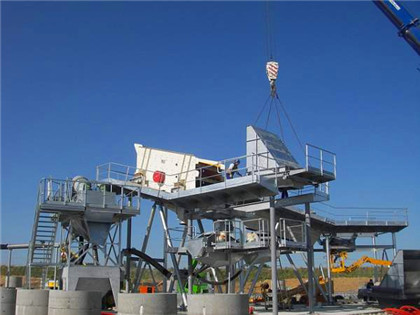
混合粉磨
反之,当矿渣掺量为%%时,混合粉磨的物料呈现硬特性,其产品粒度大于单独粉磨后再混合产品的粒度,而且粒度分布也比较宽。矿渣预挤压后与熟料混合粉磨的产品粒度分布,明显地比未挤压矿渣与熟料混合粉磨产品窄,尤其是其产品中的粗颗粒含量显著减少,表现出了体积粉碎的特征。在运动过程中,如果磨球的能量大于熟料的破坏而小于矿渣的破坏能量时,矿渣颗粒将所承受到的应力传递给周围的熟料粒子,而使得熟料粒子接受粉碎能量的几率增大,形成了一种所谓的粒子间粉碎现象,其结果是矿渣粒子促进了熟料粒子的粉碎,成为熟料粒子粉磨过程中的微粉磨介质。在混合粉磨过程中,两种组分被均匀混合,由于熟料粒子较易被粉碎,形成的细小颗粒会在矿渣料子周围形成缓冲层,从而使得矿渣粒子所接受的冲击应力减弱,粉碎几率降低,粉碎产品中粗颗粒含量上升。由于易磨性差的组分的微介质作用,使得在这些颗粒周围产生了大量的微细粒子,在粉磨过程中,这些微细粒子不但容易包覆在矿渣粒子周围,而且熟料矿渣混合粉磨,熟料破碎及图纸还由于矿渣粒子的锤焊作用而使得这些小粒子间团聚的几率上升。
不同粉磨工艺下,矿渣水泥浆体强度的差别显然是由粒度分布不同所引起的,在混合粉磨过程中,由于微介质效应而使得产品中熟料粉磨过细矿渣则较粗。由于熟料过细会使其水化速度过快,不利于成型捣实,而矿渣反应率与细度关系很大,粗颗粒将限制矿渣反应活性的发挥,因而浆体内部大尺寸孔的数量较多,导致浆体强度下降。同时,当矿渣颗粒较大时,矿渣水泥的水化相当微弱,而矿渣颗粒表面与浆体之间的粘接总是处于相对最弱处,这样浆体的断裂也往往发生在矿渣颗粒表面,这也是混合粉磨工艺生产的矿渣水泥浆体强度低的一个原因。但混合粉磨工艺可以对水泥各组分的细度作合理匹配,既可使矿渣的活性得到充分发挥,又可使熟料水化后所产生的氢氧化钙及时被矿渣玻璃体所吸收,使浆体结构的密实性增加,水泥浆体强度得到充分发展。
粉磨熟料
矿渣经预挤压后,易磨性得到了显著提高,在其后的混合粉磨过程中,产品的粒度分布可得到显著改善,从而提高了水泥浆体强度。因为从粉磨能耗粉磨工艺的简便性及粉磨产品的质量这个方面来分析,单独粉磨工艺或预挤压后混合粉磨工艺均优于混合粉工艺。但由于矿渣和水泥熟料硬度和易磨性存在较大的差异性,导致混合磨水泥中犷揸组分平均粒径较大,有研究表明在球磨机中粉磨矿渣水泥比表面积为~m/kg,其中矿渣的实际比表面积仅50~70m/kg左右,这严重制约了矿渣潜在水硬活性的发挥,在生产上则表现为矿渣掺量不能大幅度提高,或提高矿渣掺量而磨机产量降低电耗剧增。实践表明,随着矿渣粉比表面积的增大,水泥中掺人矿渣粉的比例可以适当提高,矿渣比表面积提高到m/kg以上时可大幅度增加在水泥中的掺量,可多达%左右,对混凝上的性能也有益处。为了解决这一问题,一般可采取以下措施:一是调整生料配料方案,适当降低熟料的硅酸率提高铝氧率;二是减少石膏掺人量,控制水泥中三氧化硫的含量在%左右。通过釆取以上措施,凝结时间一般比原来缩短~min,其他性能指标基本不受影响,经济效益和社会效益都很显著。单独粉磨目前,矿渣粉磨技术大致有:①矿渣与熟料石膏的共同粉磨;②矿渣单独粉磨,再与熟料石膏的细粉混合成水泥;③矿渣单独预粉磨,再与熟料石膏共同粉磨。众所周知,矿渣的水化反映滞后于水泥,要想水泥和矿渣达到同步水化目的,必缵控制冀各增不陶的细度,以充分发挥矿渣的活性,况且矿渣的硬度及耐磨性和水泥相比有很大的差别,如果矿渣不能达到理想细度,会造成矿渣对水泥的早期强度贡献小,致使混凝土及其制品的早期强度低,发展潜力不大,矿渣作为填料使用不能充分发挥活性,浪费资源。由于矿渣硬度大,难粉磨,如果要达到矿渣的理想细度,务必造成水泥熟料的过粉磨现象,使水泥的早期强度大,但发展潜力小,天强度低。
熟料矿渣
无论是矿渣不能充分利用或水泥的过粉磨现象都务必造成资源的浪费和成品成本的提高,如果采用分别粉磨的方法可以降低成本,况且可以任意调节水泥和矿渣粉的颗粒以满足于更多的要求,达到最多的颗粒级配,实现成品的多元化。
热销产品
相关资讯
栏目
- 反击破与圆锥机的比较 - 2016/12/08
- 山西忻州焦煤鄂式破碎设备 - 2016/12/08
- 生产线承包协议书 - 2016/12/07
- 淄博星形给料阀 - 2016/12/07
- 炼凡磨粉机 - 2016/12/06
- 广东惠州砂岩鄂式碎石机 - 2016/12/05
- R型雷蒙磨粉机 - 2016/12/05
- 上海振动垂直提升机 - 2016/12/04
- 丹东石英石加工一吨钢渣需要多少钱 - 2016/12/04
- 河南商丘硫黄鄂式碎石机 - 2016/12/03
- 锅炉用煤粉磨机 - 2016/12/03
- 博山锤破机 - 2016/12/02
资料下载
